
1. Introduction
Valves are critical elements inside a vessel, on whose correct operation depends on the integrity of the platform and its basic management and habitability systems, such as ballast, bilge, fire, fuel, or ventilation systems, among others.
The general increase in the automation of on-board processes, the reduction in the cost of electronic equipment, or the appearance of specific products focused on the sector have caused the percentage of motorized valves to increase notably in recent decades.
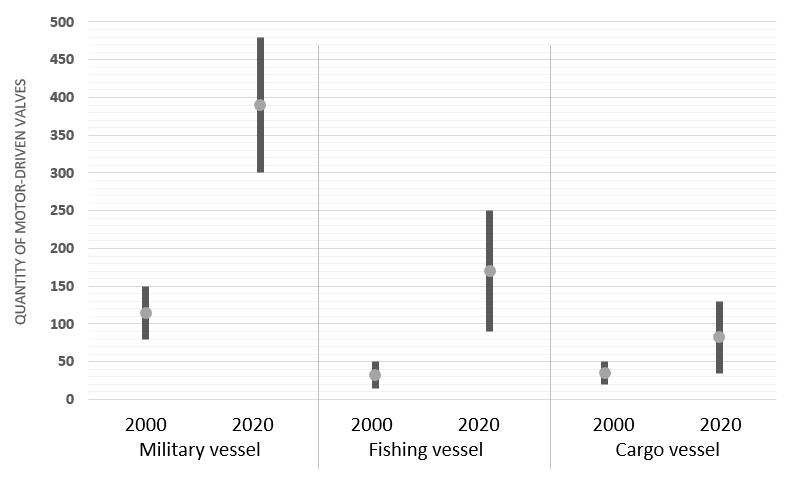
As a result, the responsibility of motorized valve systems is increasing, the associated contracts are increasingly large, and the complexity of integration has become more and more notably. All this has led to a change in the management methodology of this equipment during the shipbuilding process in recent years.
In general, motorized valves were not usually treated as a differentiated package, but the components were acquired independently by the shipyard, being in charge of the design, integration and subsequent commissioning. The integration process was simple and limited in scope, due to the small number of equipment and the little information transmitted by each one. The equipment suppliers were not highly involved in the construction process, as they did not have a clear responsibility for the collective and final functioning of their equipment.
However, currently the motorized valve system is usually understood as a main element within the design and acquisition processes of the vessels components. Its design begins early, usually in the functional engineering stage, and the purchasing process often begins in the early phases of the construction. It is common for the supplier of this system to be involved from the initial stages of design (with different degrees of implication, depending on the complexity of the vessel), and its presence is a constant from start to finish of the construction process, usually being in charge of the final commissioning of the equipment.
This change in philosophy makes it necessary for this companies to be capable of managing complex projects, have sufficient technical solvency to participate in various stages of design and production and, in general, take a step forward in the provision of services to the shipyard.
2. Components of a system of monotorized valves
A motorized valve system is generally made up of:
– Valves
– Valve actuators
– Monitoring and control system
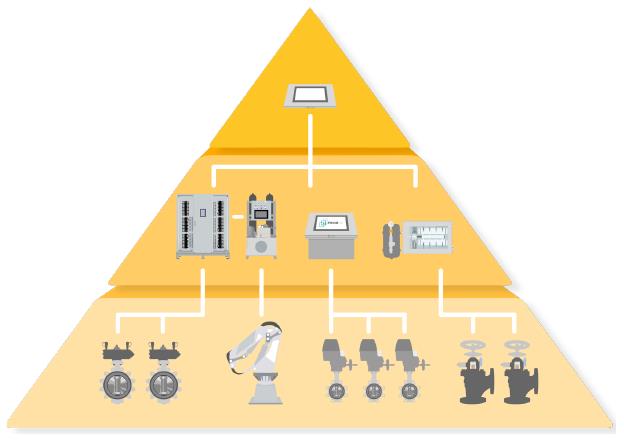
Valves
Initially, the valves to be motorized were those for critical services, such as sea chests or fire-fighting collectors, and were traditionally globe or gate valves with metal seats, which are expensive to motorize and relatively large.
Currently, most of the motorized valves on a ship are butterfly valves with elastomer seal, due to their low cost, ease of operation and good performance in most scenarios. These are also the most widespread among the ship’s manual valves, which means that, in most cases, the shipyard seeks to standardize manufacturers among manual and motor-driven valves.
The increasing focus of shipyards towards the sustainment and life cycle of ships makes the standardization and commonality of components and manufacturers essential in the purchasing process.
Actuators
Since the automation of valves in the naval sector is not as widespread as in other sectors (such as oil & gas, chemical or petrochemical, where a large percentage of the valves are motorized), until relatively recently there was not a wide variety of actuators in the market focused on use in ships or marine environments.
According to this situation, the trend has been to use actuators designed for other applications and adapt them for the use on board, resulting in two different paths, separate from each other and with a difficult intermediate point: on the one hand, the use of large actuators high sizes and weights where the requirements are higher, with functionalities sometimes oversized and costs generally high; on the other hand, the use of actuators with low performance, little robustness and very low costs, not designed to withstand the aggressiveness of the marine environment.
Faced with this growing need, in recent years there has been a notable growth in the number of actuator manufacturers that have developed specific product ranges for the naval sector. These models are usually small in size, with specific control functionalities focused on a vessel, and with a cost generally adjusted to the features required in each project. There are even manufacturers with specific ranges focused on military ships, with specific certifications against shock, vibration, or electromagnetic compatibility standards.

Monitoring and control system
Regarding the monitoring and remote control of these valves, there are different factors that influence the increased use of equipment dedicated exclusively to this task, turning motorized valve systems into subsystems for the IAS (integration and automation system of the ship) itself.
Initially, motorized valves were integrated directly into the ship’s IAS, using controls designed by the shipyard itself or integrated into control systems of other equipment (such as pump starter panels, etc.). The treatment was similar to any instrumentation element of the ship, without a specific differentiation. The number of signals to be manipulated was not very big, and the controls quite rudimentary (generally electrical logic by means of relays, etc.).
On one side, the increase in the number of motorized valves on board directly results in an increasing amount of information that must be integrated. At the same time, the evolution of actuator electronics means that they are increasingly capable of providing a greater amount of information, both for operation and diagnosis. This translates into a greater amount of data to the user, so that the number of signals that are integrated into the ship’s platform control systems is significantly increased. A system of electric motor-driven valves can involve the integration of up to 20,000 signals in the IAS. Such number of signals leads to integrate a subsystem which facilitates the incorporation of all the data in the IAS.
Another point to keep in mind is that, in recent years, there has been an evolution in marine regulations that requires greater sophistication in the control of certain equipment and systems on board. Among the systems included are ballast and bilge services, which motorized valves are critical. Examples of this are the SOLAS regulations ll-2 21, ll-2 22, ll-2 23 and ll-1 8, introduced in MSC.1/Circ.1369 (June 22, 2010) and collectively referred to as ‘Safe Return to Port (SRtP) Regulations’. These regulations apply to passenger ships built since July 1st, 2010, with a minimum length of 120m and 3 vertical levels, and they establish that certain critical systems for the navigability and stability of the ship must remain operational after a fire or flood, with the aim of achieving a safe return to port using their own means. Classification societies have issued their guidelines for the adaptation and implementation of this regulation, such as DNVGL-CG-0004 from DNV-GL, or NR 598 DT R01 E from Bureau Veritas. Within these regulations, the need for a double control of the motorized valves is exposed, which clearly points towards the need to have control systems of a certain sophistication.
At the same time, and for various well-known reasons, more and more emphasis is being placed on the cyber-security of the equipment on board, so as to minimize the risks of compromising the security of the ship due to a cyber-attack on the management systems. This is evidenced in IMO circulars such as MSC.1/Circ.1526 (June 1, 2016) or MSC-FAL.1/Circ.3/Rev.1 (June 14, 2021), and various recommendations and adaptations made by societies of classification. Since the motorized valves manage critical services for the survival of the ship, the automation systems that manage them are not exempt from including security mechanisms that limit these threats as much as possible.
Since the IAS is a clear target for any possible cyber-attack, a strategy followed more and more often is, again, segmentation into subsystems. In this way, in the event of a possible general cyberattack that disables or limits control from this system, healthy subsystems can be isolated and manipulated independently. This aspect also enhances the use of control systems dedicated to motorized valves.
As a result of all the above, the need for a more complex, sophisticated, robust, and safe valve control is evident, resulting in the appearance of specific commercial solutions for the naval sector, something that was not usual before.
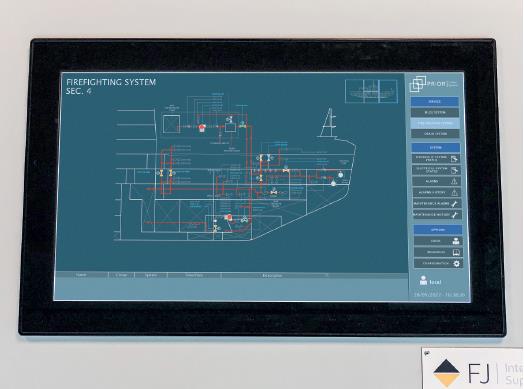
3. Near future of motorized valve systems
The levels of automation of the ship are becoming higher, even developing projects for fully autonomous ships (the IMO has even published preliminary guidelines on the testing of these ships, among others in the publication MSC.1/Circ.1604 of the June 14, 2019). It is therefore expected that the level of valve automation will also gradually continue to increase, at a similar rate to that of recent years. The classification societies themselves are expanding and reviewing the requirements on motorized valves, actuators of various types (there is still discrepancy between the CCSS on the specific requirements to apply to electric actuators, for example) and associated control systems.
The inclusion of new technologies (such as the digital twin or additive manufacturing) and new requirements, especially in terms of security (including the cybersecurity of systems), will have an important role in shipbuilding and, therefore, in these systems.
In this framework, companies like ours, Fernández Jove, that can offer end-to-end solutions, integrating (or even manufacturing) the different components that compose a motorized valve system, take on special importance.